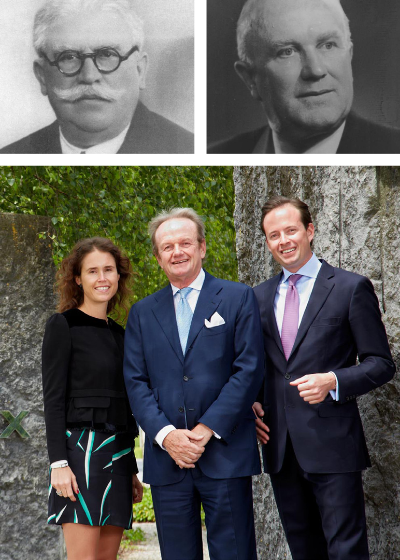
THE STORY OF A 100-YEAR-OLD COMPANY
This is the story of a 100-year-old company and four generations of the Schmitz family, whose collective entrepreneurship has faced numerous challenges and found solutions to match.
There was never a question of Rotarex (formally Ceodeux) limiting itself to a handful of products or markets. This family business has always striven to innovate its products and production processes, and worked hard to expand a global client base.
This approach enabled the firm to adapt to the numerous economic, social and geopolitical changes which have marked the last century. Openness and innovation were also required when managing acquisitions of international businesses, moves which often led to changes in processes and client relationships.
Rotarex is a Luxembourg company with a global presence. It has nine business units, over 30 sales offices across five continents, with our valves, regulators, and gas control systems sold in more than 150 countries.
The workforce is nearly 2,000 strong, of whom 900 are in the Grand Duchy of Luxembourg. Annual sales will approach €300m in 2022. 3% of the value of this turnover is invested annually into research and development. Spending on new equipment totals around €15M every year.
This investment comes alongside the construction of our new 40.000 m2 plant and headquaters in Bissen scheduled for completion in 2024, and the investment in a new 7,000m2 factory in South Korea.
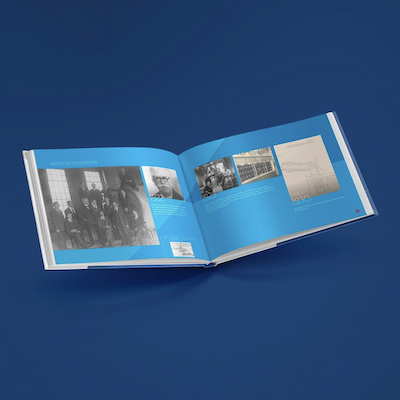